吳遠彬1,陳志強1,陳金明2,劉曉輝1,劉月蓉1
(1·福建省林業科學研究院,福建福州350012; 2·福建省林業科學技術推廣總站,福建福州350003)
摘要:UF-G低毒脲醛樹脂在膠合板上的應用研究結果表明,最佳調膠參數為面粉添加量25%,固化劑添加量1·2%;最 佳熱壓工藝參數為熱壓溫度110℃、熱壓壓力1·2 MPa、熱壓時間60 s·mm-1、涂膠量300 g·m-2。在此條件下壓制出的膠合板甲醛釋放量達到E1級,且膠合強度滿足國家標準的要求。
關鍵詞:低毒;UF-G;脲醛樹脂;膠合板
中圖分類號:TS653·3 文獻標識碼:A 文章編號:1002-7351(2007)02-0028-04
UF-G低毒脲醛樹脂膠是國家林業局推廣項目“UF-G低毒粉狀脲醛樹脂膠的推廣應用”的科研成 果,其制備原理是采用堿-酸-酸-堿生產工藝,甲醛分2次投入,尿素分3次投入,并且加入增強劑與脲 醛樹脂共縮聚。利用此原理制備出的UF-G脲醛樹脂與普通脲醛樹脂相比,具有甲醛含量大為降低,同 時利用其生產出的產品的強度不會有明顯的下降。本文對UF-G低毒脲醛樹脂在膠合板生產中應用進 行研究,從調膠工藝和熱壓工藝等參數進行大量試驗,確定出最佳工藝參數,生產出的膠合板甲醛釋放量 可直接達到E1級、同時膠合強度能滿足國家標準要求。
1 試驗材料和設備
1·1 試驗材料
1·1·1 UF-G脲醛樹脂膠 實驗室自制,其性能指標為:固含量62%±3%,密度1·215 g·cm-3,pH值8 ~9,粘度240~160 CP,固化時間50~65 s,游離甲醛含量≤0·15%。
1·1·2 馬尾松單板 取自直徑為25~30 cm的馬尾松原木,厚度2·3 mm。
1·1·3 復合型固化劑 組分為15%氯化銨和3%草酸。
1·1·4 工業面粉。
1·2 試驗儀器及設備
QD型試驗熱壓機(濟南試金集團有限公司),RGT-30型電子力學試驗機(深圳市瑞格爾儀器有限公 司),SP-2100型可見光分光光度計(上海光譜儀器有限公司),NDJ-1旋轉式粘度計(上海天平儀器廠), DHG-9023A型電熱鼓風干燥箱(上海精宏試驗設備有限公司),JJ-500型電子天平(常熟市雙杰測試儀 器廠)。
2 試驗方法
2·1 膠合板試驗工藝流程

2·2 檢測方法
2·2·1 甲醛釋放量 按GB 18580—2001中9~11 L干燥器法進行測定。
2·2·2 膠合強度 依據膠合板國家標準GB/T 17657-1999中膠合強度測定方法。
3 結果與分析
3·1 UF-G脲醛樹脂調膠工藝參數水平的確定
3·1·1 面粉添加量與粘度的關系在調膠時加入一定量的面粉,可增加膠液的固含量、粘度和初粘性,改善板的預壓性能,同時可以節約膠料,降低成 本。對面粉添加量與調膠后脲醛樹脂膠粘度的關系進行試驗,以便從中選擇出適合于膠合板生產工藝要求的粘度范圍,結果見圖1。

經過試驗發現,在調膠后,膠液的粘度范圍 600~900 CP之間,施膠效果較好。根據圖1可知 面粉添加量范圍為20%~30%滿足要求。
3·1·2 調膠參數試驗
試驗以調膠時面粉添加量、單板含水率和固化劑添加量為因素,試驗設計 采用3個水平,見表1;利用L9(34)正交試驗表進 行膠合板壓制試驗,每一試驗都統一采用以下熱壓 工藝參數:熱壓溫度105℃,涂膠量280 g·m-2(雙 面)。熱壓壓力1·0 MPa,熱壓時間1 min·mm-1 陳化時間20 min。壓制出的試件為5層結構,厚度 8~9 mm。
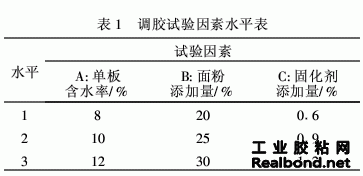
將壓制好的膠合板放置7d后,根據標準方法測定每塊板的甲醛釋放量和膠合強度,并進行極差分析,結果見表2。
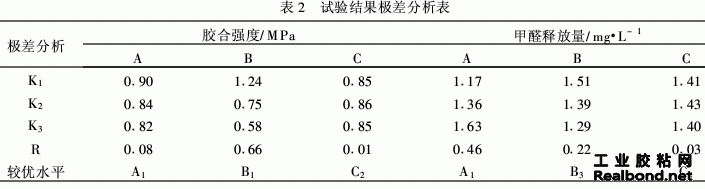
3·1·3 調膠試驗結果與分析 ①面粉添加量的影響:從極差分析上看,面粉添加量對膠合強度影響最大, 隨著面粉添加量的增加,膠合板的膠合強度呈下降趨勢。但面粉的添加量提高,減少了脲醛樹脂的用量, 有利于降低甲醛含量。從試驗結果上看,當面粉填加量在25%左右時,既能保證低甲醛釋放量,又能滿足 強度要求。②固化劑填加量的影響:從表2可知,固化劑添加量對膠合板的膠合強度和甲醛釋放量的影響 并不明顯,但在實際操作中,對膠合板的預壓效果有較明顯的影響,因為預壓效果取決于膠液調膠后的粘 度和濃度,固化劑添加量大,在溫度低的情況下,有較大優勢,它能在短時間內發揮作用,使膠液達到一定 粘度,相對于低添加量,更能明顯改善板坯預壓效果的。③單板含水率的影響:單板含水率是影響甲醛釋 放量的最主要因素。隨著原料單板含水率的提高,產品的甲醛釋放量明顯增加,單板含水率從8%提高到 12%時,膠合板甲醛釋放量由1·17 mg·L-1增加至1·67 mg·L-1,單板含水率除了甲醛釋放量有影響外。 對膠合強度也有一定的影響。單板中含有過多的水分,會影響膠粘劑分子量增長和粘度提高的速度,使膠粘劑過度向單板內部滲透,造成膠接質量下降,膠合強度降低,因此單板含水率不應太高。
3·2 膠合板熱壓工藝參數確定
在熱壓工藝參數研究中,采用正交試驗法進行分析,選定的影響因素4個:熱壓壓力、熱壓溫度、熱壓 時間和涂膠量,制定了3個水平(見表3),選用L9(34)正交試驗表進行試驗,在試驗中,單板含水率為8%, 面粉添加量為25%,固化劑添加量為1·2%。

為了便于分析各因素對性能的影響趨勢,根據正交試驗所壓制的膠合板進行檢測,測定結果繪制了極 差分析圖(圖2),從圖中可以較直觀地看出,熱壓工 藝參數對板材甲醛釋放量和膠合強度的影響趨勢。
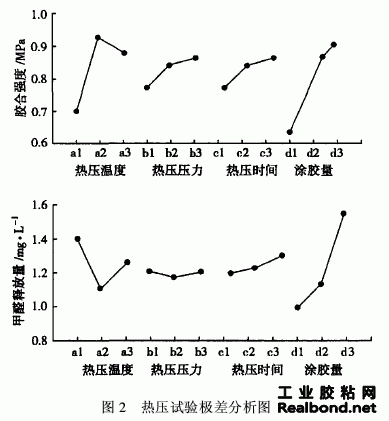
3·2·1 熱壓溫度的影響
從圖2可知,熱壓溫度對 膠合強度和甲醛釋放量的影響還是比較大的。在本 試驗研究的水平內,當熱壓溫度100℃時,膠合強度 最低,在此溫度下,因為脲醛樹脂膠的固化不充分, 膠合強度降低,甲醛釋放量也高。隨著熱壓溫度的 上升,膠合板的膠合強度開始明顯上升,在110℃時 達到最高值,當溫度達到120℃后又逐漸下降。因 此在本試驗條件下,熱壓溫度選用110℃比較理想。
3·2·2 熱壓壓力的影響
隨著壓力的增大能夠使膠合板的膠合強度明顯提高,但隨著壓力增加到一 定程度,膠合強度增加的幅度減小,并且板材的壓縮 率增大,出材率降低。從甲醛釋放量上看,過高的壓 力和過低的壓力都會使甲醛釋放量略有提高,但并 不顯著。根據上述綜合來看,在試驗中,熱壓壓力為 1·2 MPa時,強度已經達到國家標準的要求,且甲醛 釋放量較低。因此在此參數中選擇熱壓壓力為1·2 MPa。
3·2·3 熱壓時間的影響
試驗結果顯示,隨著熱壓時間增加,膠合強度和甲醛釋放量都呈現增長勢態,但 整體增長趨勢較為緩慢。熱壓時間再延長,雖然板材的膠合強度沒有明顯的降低,但板材的壓縮率會增 大,使出材率降低,另一方面,熱壓時間長,導致膠層受熱太久,而發生降解,使得板材的甲醛釋放量也相應 升高。因此在本試驗條件下,熱壓時間選用60 s·mm-1較為適當。
3·2·4 涂膠量的影響
從試驗中可知,涂膠量對膠合板的膠合強度影響和甲醛釋放量的影響是十分顯著 的,隨著涂膠量的增大,產品的膠合強度明顯增大,當涂膠量為300 g·m-2時,其膠合強度已經達到較高的 程度,當涂膠量超過300 g·m-2后,板材的膠合強度雖有所增加但不明顯,這樣從成本上算性價比不高,而 且由于膠層變厚,試驗時容易透膠,固化后應力增大,會影響膠合板的質量,從試驗上看,壓制膠合板時,要 使膠合板的膠合強度達到國家標準的要求,涂膠量控制在300 g·m-2左右就可以了,這樣甲醛釋放量也較低,同時有利于生產成本的降低。
4 結論
1)使用UF-G低毒液狀脲醛樹脂壓制膠合板,其最佳調膠參數為面粉添加量25%,固化劑添加量 1·2%,最佳熱壓工藝參數為熱壓溫度110℃、熱壓壓力1·2 MPa、熱壓時間60 s·mm-1、涂膠量300 g· m-2。這樣壓制出的膠合板甲醛釋放量達到E1級,且膠合強度滿足國家標準的要求。
2)涂膠量增大,膠合強度明顯增大,當涂膠量超過一定量后,板材的膠合強度有所增加但不顯著,而甲 醛釋放量則隨著施膠量的增加而明顯增加。
3)增大熱壓壓力能使膠合板的膠合強度得到較明顯提高,隨著壓力的繼續增加,膠合強度增加的幅度減小。過高的壓力和過低的壓力都會使甲醛釋放量略有提高,但并不明顯。
4)熱壓溫度對膠合強度和甲醛釋放量的影響也十分明顯,隨著熱壓溫度的上升,膠合板的膠合強度會有明顯上升。但過高的溫度會使固化的膠層發生熱降解,使膠合強度逐漸下降,甲醛釋放量明顯提高。
5)熱壓時間對膠合強度和甲醛釋放量的影響不是很明顯,隨著熱壓時間增加膠合強度和甲醛釋放量都呈現增長勢態,但整體增長趨勢較為緩慢。
參考文獻:
[1]王茂元,仇立干,周秋華·低毒耐水脲醛樹脂膠粘劑的生產及其應用[J]·化學建材,2002(4):33-44·
[2]吳羽飛,顧海英·楓木膠合板的實驗室制造工藝[J]·林業科技開發,2004,18(5):27-29·
[3]陳桂華,劉碧華,吳湘娟·泡桐膠合板生產工藝研究[J]·林業科技,2003,28(6):33-35·
[4]董玉香,商成臣·膠合板生產工藝對產品質量的影響[J]·林業科技通訊,2000(6):4-6·
[5]沈哲紅,李文珠,方 群·提高低甲醛釋放膠合板膠合強度的研究[J]·林產工業,2003,30(6):22-26·
[6]朱麗濱,顧繼友,翁向麗·脲醛樹脂固化特性對膠接性能、甲醛釋放量的影響[J]·東北林業大學學報,2004,30(2):32- 34·